Are you a newbie in plumbing or a plastic lover? If so, you must be eager to learn more about the comparison between hepd and pvc. Because of their similar or close appearance, it is easy to confuse them.
In this article, we provide you with a comprehensive comparison and contrast between these two competing pipes to help you make the best choice.
Before we go deeper, let’s explore the differences in their descriptions.
HDPE & PVC – Definitions.
Understanding Hdpe
HDPE is a thermoplastic resin formed by low-pressure polymerization of ethylene monomers (such as Ziegler-Natta catalysts). It is the highest density (0.940–0.970 g/cm³) subclass of polyethylene (PE). The molecular structure is linearly arranged, the crystallinity is 80%~90%, and the molecular chain interaction is strong
HDPE has high hardness, tensile strength (20-35 MPa) and wear resistance, but weak resistance to environmental stress cracking
Understanding PVC
PVC is a thermoplastic formed by free radical polymerization of vinyl chloride monomer (CH₂=CHCl). The molecular chain contains polar chlorine atoms, with a density of about 1.35–1.45 g/cm³ and a chlorine content of up to 56.8%, giving it self-extinguishing properties (flame retardant value > 40)
PVC is a chlorine-containing polar polymer, characterized by flame retardancy, low cost, and adjustable hardness, and is suitable for conventional civilian scenarios
HDPE vs. PVC – Key Differences
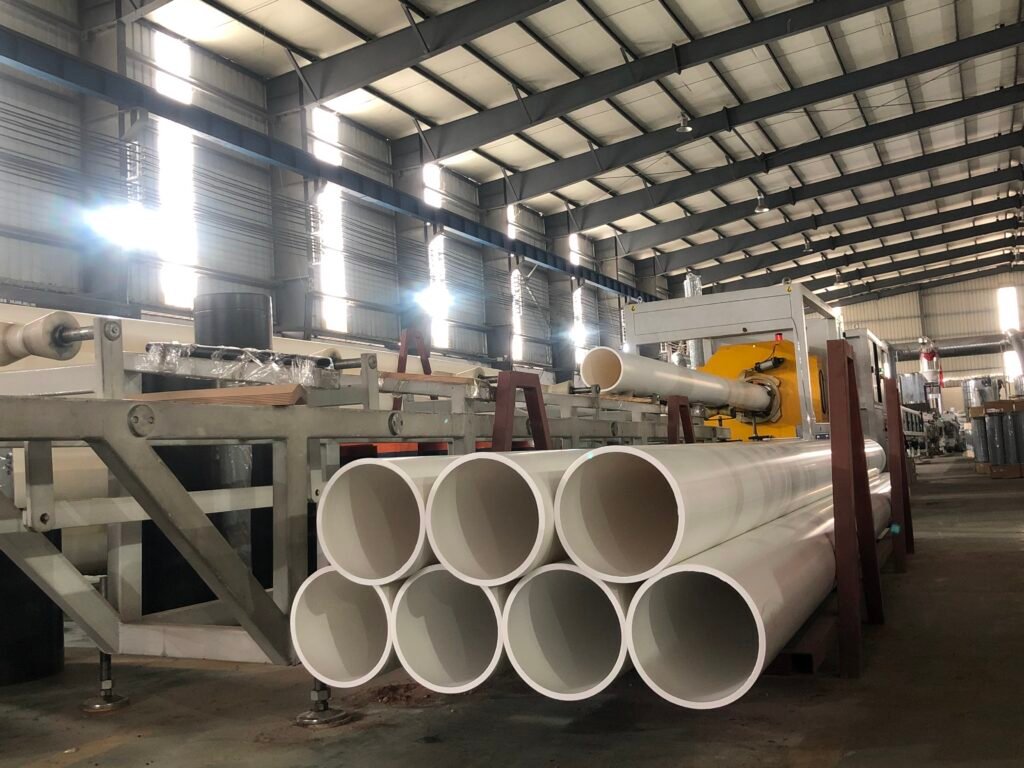
Chemical structure differences
HDPE (high-density polyethylene) is formed by polymerization of ethylene monomers, and its molecular chain is linear with almost no branches.
PVC (polyvinyl chloride) is formed by polymerization of vinyl chloride monomers, and its molecular chain contains chlorine atoms (-Cl). It has fewer branches, but the structure is more polar due to the presence of chlorine atoms.
Differences in molding methods
HDPE processing methods: injection molding, blow molding, extrusion molding.
PVC processing methods: injection molding, extrusion, calendering, blow molding, etc. Different additives (such as plasticizers, stabilizers) need to be added according to the purpose.
Environmental Differences
PVC contains chlorine, and releases toxic gases such as hydrogen chloride and dioxins when burned; vinyl chloride monomer (carcinogen) may remain during the production process, and plasticizers (such as phthalates) in soft PVC may migrate into food or the environment.
HDPE does not contain chlorine, and produces carbon dioxide and water when burned, with almost no toxic gases (but low-toxic monomers may be released at high temperatures).
Differences in physical properties
HDPE is soft at room temperature and suitable for making flexible products. It is resistant to acids, alkalis and organic solvents.
PVC soft PVC is flexible, while hard PVC is hard and brittle. It is resistant to acids and alkalis, but not to solvents such as aromatic hydrocarbons and halogenated hydrocarbons.
Differences in application areas
HDPE is mainly used in construction and pipelines, underground water pipelines (strong corrosion resistance), and gas pipelines.
PVC is mainly used in building materials: door and window profiles, water pipes (hard PVC), and floor coverings (soft PVC).
HDPE vs. PVC– Advantages and Disadvantages
Advantages of HDPE
Here are some of the advantages you will derive from HDPE:
Good mechanical strength and toughness
It has a high density (0.941-0.965 g/cm³), a dense structure, and is both rigid and flexible. It has strong impact resistance (it can maintain toughness even at low temperatures), and is suitable for manufacturing products that need to bear weight or resist falling (such as trash cans and industrial containers).
Strong chemical corrosion resistance
It has good tolerance to acids, alkalis, salt solutions and most organic solvents (such as alcohols, aldehydes, and ketones), is not easily corroded by chemicals, and is often used in corrosion-resistant scenarios such as chemical storage tanks and pesticide packaging bottles.
Excellent anti-aging performance
The molecular structure is stable and is not easily degraded by ultraviolet rays, oxygen or moisture in the natural environment. It has a long outdoor service life (for example, underground water pipes can be used for more than 50 years).
Non-toxic and low-pollution
The chemical composition does not contain harmful substances such as chlorine and heavy metals. The products (such as food-grade HDPE containers) meet food safety standards and can directly contact food, with high safety.
High cost performance
No complex additives are required during processing, the overall cost is controllable, and the product is durable and has a long-term use cost
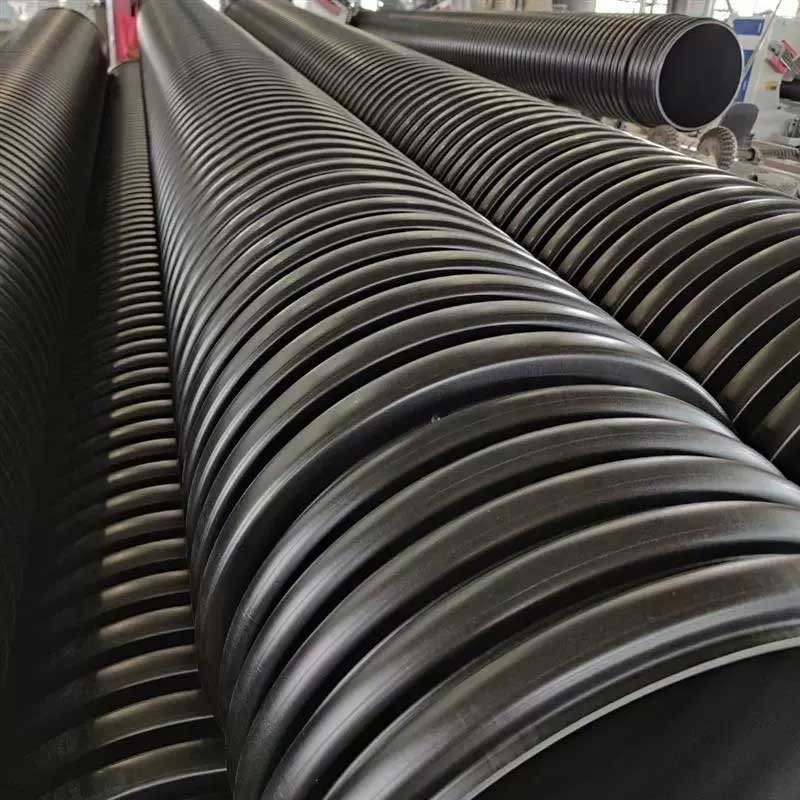
Disadvantages of HDPE
Insufficient rigidity and hardness
Compared with PP (polypropylene) or engineering plastics (such as ABS), HDPE has weaker rigidity and its products are prone to “soft collapse” (such as thin-walled containers are prone to deformation when bearing loads). It is not suitable for manufacturing structural parts that require high hardness (such as mechanical housings and high-strength tools).
Limited resistance to UV aging
Long-term exposure to sunlight (especially in an environment with strong ultraviolet rays) will gradually break the molecular chains, causing the products to become brittle and fade (for example, if antioxidants and ultraviolet absorbers are not added to outdoor HDPE pipes, the service life may be shortened to less than 10 years).
Poor antistatic properties
It has strong insulation properties and is prone to static electricity due to friction. It is not suitable for manufacturing electronic component packaging materials (extra antistatic agents need to be added) or for use in flammable and explosive environments (such as gas station pipes, which need to be used with caution).
Advantages of PVC
Here are some of the advantages you will derive from PVC:
Outstanding weather resistance and aging resistance
It has a certain UV resistance. After adding stabilizers (such as lead salts, calcium-zinc composite stabilizers), the outdoor service life can reach 10-20 years (such as PVC door and window profiles have better weather resistance than wood and are not easy to fade or deform).
Good surface treatment performance
The surface polarity is high, the ink adhesion is strong, and it can be directly printed without additional pretreatment (such as color printing of plastic cards and packaging boxes); it has good compatibility with glue and coating, which is convenient for surface decoration (such as film treatment of PVC floor).
Excellent electrical insulation
With a volume resistivity of 10¹³-10¹⁶Ω・cm and a low dielectric constant, it is an ideal insulating material (such as the insulation layer of wires and cables, and the housing of electronic components) and is safer than ordinary rubber.
Low cost of raw materials
The raw materials for production mainly come from petroleum and limestone (through the polymerization of vinyl chloride monomer), and the price is lower than polyolefin plastics such as PE and PP. The cost advantage is significant, especially in large-scale production (for example, the price of PVC pipes is 10%-20% lower than that of HDPE pipes).
Diversified applications of packaging and daily necessities
Disadvantages of PVC
Weak impact resistance
After the plasticizer migrates or volatilizes (such as soft PVC products used for a long time), the material will become hard and brittle, and the performance will deteriorate (such as cracking of aging PVC wire sheath).
The process is complex and energy-intensive
It is necessary to add a variety of additives (stabilizers, plasticizers, lubricants, etc.), the formula is difficult to debug, and the production process is more complicated than HDPE (for example, PVC pipe extrusion requires precise control of temperature and pressure to avoid decomposition).
Low recycling value
The performance of recycled PVC materials has declined significantly and they can usually only be used to produce low value-added products (such as shoe soles and building material fillers). However, recycled HDPE materials can be reused in pipes, containers, etc., and are more economical to recycle.
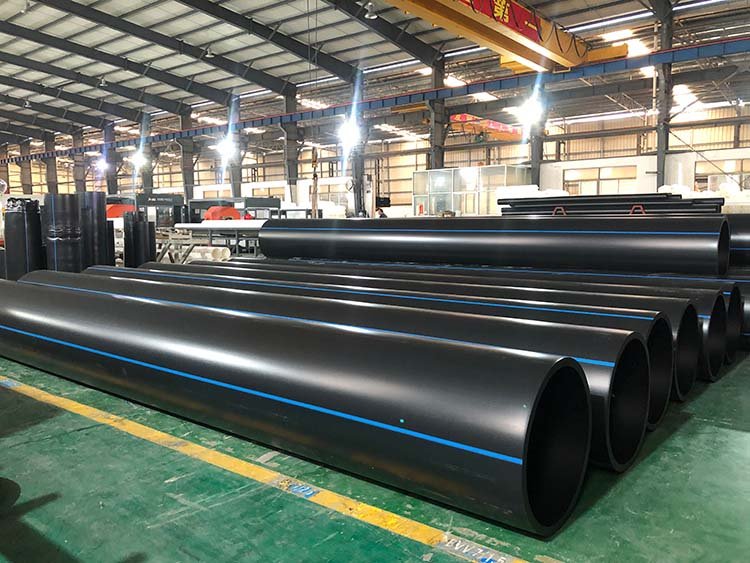
HDPE vs. PVC – Industry Applications
Typical Applications of HDPE
- Packaging area: milk bottles, detergent bottles, food packaging bags (low temperature resistant).
- Buildings and pipelines: underground water pipelines (strong corrosion resistance), gas pipelines.
- Daily necessities: trash cans, plastic cutting boards, toys.
- Industrial field: chemical containers, impermeable membranes (such as landfill liners).
Typical Applications of PVC
- Building materials: door and window profiles, water pipes (rigid PVC), floor coverings (soft PVC).
- Packaging materials: plastic wrap (soft), medicine packaging box (hard and transparent).
- Daily necessities: artificial leather, plastic sandals, inflatable toys.
- Industrial field: insulation layer of wires and cables (voltage resistance), anti-corrosion pipelines.
결론
The core difference between HDPE and PVC lies in the presence or absence of chlorine in the molecular structure, which directly affects the physical properties, processing methods and application scenarios of the two. HDPE is known for its weather resistance, chemical resistance and environmental protection, and is mostly used in packaging and pipes; PVC can be adjusted to meet different soft and hard requirements through additives, but there is a lot of environmental controversy, and it is mainly used in construction and daily necessities. In actual applications, appropriate materials can be selected based on performance requirements, cost and environmental requirements.